Recycling concrete wastewater: a sustainable and cost-effective solution for the construction industry
- 6 January 2025
- Posted by: Emelyne CHEVALIER--SEURE
- Category: Recycling
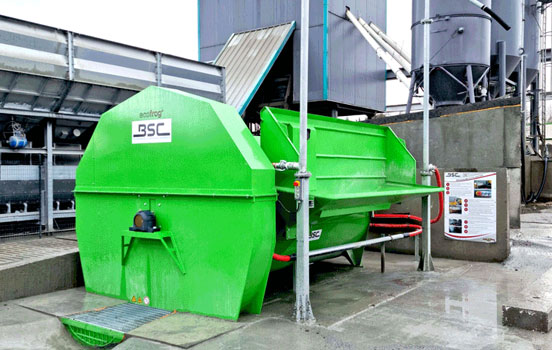
In 2023, concrete production totalled around 22 million tonnes. This quantity demonstrates the importance of concrete and its popularity in the construction industry, with widespread use in various infrastructure and building projects. Unfortunately, a significant amount of concrete remains in the mixer drum, representing a large amount of residual material that is not recycled. The production of concrete consumes a lot of energy and water, making it one of the industries producing the most CO2, accounting for 5% of emissions worldwide. Concrete wastewater with a high pH is often considered as waste that can only be disposed of in specific treatment centres. For several years now, all of this waste has been recyclable and reusable, offering a sustainable solution for reducing the environmental impact of this industry.
Why recycle concrete wastewater?
The production of concrete is a major source of pollution for our ecosystem. The European standard governing the recycling of concrete wastewater is EN 1008:2002. In France, the recycling of concrete wastewater is governed mainly by standard NF EN 1008. This standard specifies the requirements for the use of water, including recycled water, in the manufacture of concrete. It covers sampling, testing and assessment of the suitability of water as an additive in concrete.
This standard is essential to ensure that the water used does not compromise the quality of the concrete produced, and that it complies with environmental and safety criteria. To limit the degradation of our environment, the concrete industry is encouraged to find solutions
Concrete wastewater comes mainly from equipment cleaning operations, concrete surpluses and mixing processes. This water can contain particles of cement, sand and chemical admixtures, making it complex to treat and dispose of. Without proper and rigorous management, it can pollute water resources and contribute to environmental degradation.
What’s more, recycling the waste water from the treatment of concrete residues and non-compliant concretes not only allows the water to be returned to the water mains, but also generates savings from the cost of disposing of the cakes, which can be reduced to a powder and reused in concrete production, while ensuring the right balance of materials in the recipes, as the Berding Beton group points out. Once the water has been recycled, it can also be reinjected into the production circuit and used to wash equipment, particularly mixer tanks.
Government and European standards are pushing for the creation of concrete wastewater recycling schemes to serve the ambitions of creating a virtuous cycle.
In the same way, concrete manufacturers can now have a treatment cycle to recover products after recycling and have a production unit that generates zero waste
The challenges of recycled concrete wastewater
Recycling waste water is very important for better management of water resources and savings in raw materials.
Water quality
Recycled water must meet strict quality standards, particularly in terms of pH, chloride and sulphate content, so as not to compromise the properties of the concrete. If the recycled water is to be discharged into the sewer system, it must have a pH of between 6.5 and 9.5. If the water obtained from recycling is of poor quality, this can compromise the mechanical properties and durability of the concrete produced.
The density of the charged water
Depending on the stage of recycling, the contaminated water can be reused in the composition of the concrete recipe, taking into account the M.S. content (chlorides and sulphates in particular) in the water and the density of the water. In addition, depending on the final objectives of concrete production, concrete consistencies can vary between manufacturers. Indeed, for KUTTER GmbH & Co KG, the perfect consistency for concrete, the density of the concrete water must imperatively be between 1.05 and 1.06, as Wolfgang Mayer, Head of Technology and Fresh Concrete at the Darast site in Woringen, points out. As for fdu technology expert Ulrich Meier, his research shows that a constant density of 1.01 to 1.02/litre is recommended to obtain the best concrete consistency.
If the density of the residual water is too high in M.S. according to the reference indices for the constitution of concrete, then residues are deposited in the water pipes and in the water balance, which is a major drawback in the production of concrete. As a result, the entire system becomes clogged. In addition, if the sediments are too dense, the workability of the concrete will be more limited and its strength will be lower than a concrete with a traditional composition (binder + pure water).
Presence of contaminants
Contaminants such as cement residues or fine particles can alter the quality of the recycled water and therefore the quality of the concrete produced. These contaminants can affect the chemical composition of the mixing water and thus reduce the quality of the concrete. For this reason, it is crucial to put in place effective treatment systems to eliminate these impurities so as not to compromise the performance and quality of the concrete.
Cost of concrete wastewater treatment technologies
The technologies required to treat and recycle concrete residue wash water can be costly, which may represent an obstacle for some companies, but we can see it as a viable and economical long-term investment. When we calculate the costs, we quickly realise the savings made by reusing concrete waste water and reducing M.S. and cement consumption. Take the example of fdu, a German manufacturer of reinforced concrete precast slabs and pre-cast concrete walls, which is making significant savings on cement purchases: 650 tonnes of cement and 360 tonnes of CO2 per year. Thanks to the recycling system put in place by our supplier, AJF, the company is reducing its waste removal costs, particularly since almost all the waste is reused in the production of concrete. If the CWAS, AJF’s patented filter press, is used, all the waste water can be reused again and again.
Strict regulations
The use of recycled water in concrete production is subject to strict regulations. The aim of these regulations is to ensure that recycled water does not adversely affect the quality of the concrete or the safety of the structures being built. Meeting these standards can be complex and requires ongoing monitoring and regular testing.
Quality variability
The quality of recycled water can vary depending on the original materials and the recycling processes used. This variability can affect the consistency and performance of the concrete produced. It is therefore crucial to rigorously control the recycling process to ensure consistent water quality.
How can concrete wastewater be recycled?
Recycling concrete wastewater is essential to reduce the environmental impact of concrete production. Standards have been introduced by the European Union and the French government in response to the importance of preserving the environment.
There are a number of solutions for meeting the standards required to protect the ecosystem:
- The washer or settling tank,
- The filter press,
- The sand filter microfiltration plant,
- The CO2 pH neutralisation system.
The concrete residues from the cutter trucks or from production are introduced into the washer (RE_X), or into the settling tank. Once the elements have been separated, the contaminated water is stored in a tank fitted with an agitator to keep the suspended particles in suspension. The water containing these fine particles (M.S.) is then transferred to the filter press (CWAS).This recycling system separates the minerals smaller than 250 microns from the water and compresses them into pebbles1. The water is filtered and becomes clear thanks to the filter bags, the filter press. At this stage, the water is still unsuitable for discharge into watercourses or water mains. It can be used for cleaning mixing tanks or for producing concrete. On the other hand, much of the sediment can be reused in recipes at this stage of water recycling. An innovative cement-water treatment, such as the CWAS patented by AJF, ensures low density of the water recycled from the concrete throughout the year. This allows the residual water to be used up to 100%, guaranteeing excellent concrete quality while creating a continuous cycle.
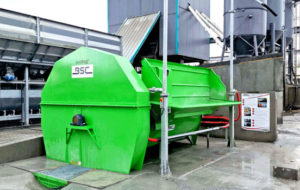
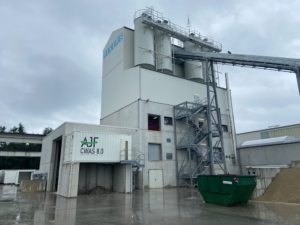
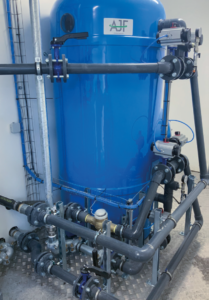
If the water is to be re-injected into the water mains or specific networks, the last fine particles in the water need to be treated using the sand microfiltration station. Almost 90% of suspended particles larger than 40 microns, such as sand, cement or oxidised iron, are eliminated. The filtration process takes place in a pressurised tank, where the quartzite undergoes progressive saturation. When the water is completely free of particles and the sand filter is saturated with dirt, the microfiltration station cleans itself automatically. The water then circulates through the column, restoring the initial operating conditions.
At this stage, the water is still unfit for discharge into the U.S. because the pH is still rated at 13, whereas environmental standards require it to be between 6.5 and 9.5. This is because the active cement has a considerably alkaline value. Water can be treated to achieve this pH:the CO2 pH neutralisation system. This system consists of purifying the water and achieving a pH so that the water can be reintroduced into the sewage system or the ecosystem. In general, alkaline wastewater can be neutralised by acids. CO2, by forming carbonic acid when it comes into contact with water, neutralises alkaline water through various chemical processes. Its use is particularly effective for concrete wastewater, as a buffer system is formed to reduce the risk of overdosing. No harmful substances are produced using this environmentally-friendly method.
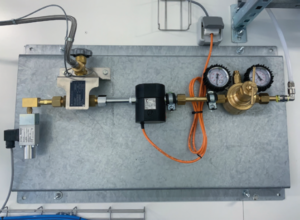
Following this treatment, the water can be returned to the local wastewater circuit or reused directly in the concrete process stages, as indicated in the report produced by AJF for one of its customers equipped with this concrete wastewater treatment system. The Berding Beton group reports significant savings thanks to the reuse of water in its concrete process and the clearly lower disposal costs for filter cakes generated by the installation of AJF’s complete system (filter press, sand filter microfiltration station and CO2 pH neutralisation system). What’s more, it allows the company to assume its share of ecological responsibility. According to studies, by recycling concrete wastewater, source water consumption can be cut by around 17-20%, and cement use is reduced.
1 The cakes can be reduced to powder and reintroduced into concrete recipes without altering the superior quality of the concrete.
The concrete industry has had to reinvent itself in the face of environmental and economic challenges, thanks in large part to European and government standards. This has led to the emergence of new sectors, such as concrete and wastewater recycling. These initiatives have proved effective in preserving the ecosystem around industrial sites, and have reduced the costs associated with water supply and the disposal of concrete waste. However, recycling concrete water presents significant challenges, such as water quality management, contaminant removal, treatment costs, regulatory compliance and quality variability. With innovative solutions and rigorous management, it is possible to maximise the environmental and economic benefits while minimising the drawbacks.